Exceptional versatility in tube sheet re-lining
SÄKAPHEN Si 57 E, Si 57 E/RE
SÄKAPHEN HR 60 Extra TG
At an authorized applicator. In a customer’s workshop. Or directly on-site. No matter where it takes place, the application of our re-lining products for tube sheets always guarantees a durable, cost-effective method to protect newly fabricated and already existing heat exchangers, condensers and coolers against corrosion and erosion as well as abrasion caused by challenging process conditions and also galvanic corrosion due to dissimilar metals
For this complex field of application, SÄKAPHEN has developed several different coating and lining solutions to meet any requirement, regardless of the service conditions, substrate materials and types of job – tube-side lining, shell-side coating or coating of tube sheets only.
Tube sheets, in particular, are the most exposed part of a heat exchanger. SÄKAPHEN has fine-tuned various procedures and solutions to repair wear and tear on coated tube sheets’ surfaces after years of operation, as shown by these three interesting success cases.
SUCCESS CASE #1: Re-lining of tube sheets after retubing
Product used: Si 57 E
Operation performed: Authorized Applicator
A small heat exchanger operating at temperatures around 120 °C was subjected to retubing. The customer specified the application of a tube sheet coating to prevent galvanic corrosion between the carbon steel tube sheet and the alloy tubes. SÄKAPHEN’s Si 57 E baked epoxy-phenolic product was selected because it can perfectly withstand both the slightly elevated pH, as the medium was conditioned cooling water, and temperature (120 °C). SÄKAPHEN applied it in-house due to the operation’s requirements in terms of baking technical equipment.
SUCCESS CASE #2: Re-lining of a chiller unit’s tube sheet
Product used: Si 57 E/RE
Operation performed: on-site
A chemical facility’s chiller unit, installed within the production train and handling cooling water below 70 °C, had been lined with heat-cured Si 57 E both on the tube side of the heat exchanger and subsequently on the tube sheet as well. After several years, the tubes’ lining was still in very good condition, but the tube sheet showed the expected signs of wear and tear. The on-site recovery operation carried out by SÄKAPHEN and a local subcontractor included cleaning, shot blasting and re-coating with Si 57 E/RE. It only took 4 days to complete it.
SUCCESS CASE #3: Re-lining of a damaged refinery tube sheet
Products used: Ceramoclad 221 and HR 60 Extra TG
Operation performed: at the customer’s premises
A tube bundle was taken out of the production train for cleaning and inspection. After inspection by SÄKAPHEN it was confirmed that the lining inside the tubes was still in good condition. However, during the dismantling of the water boxes, deeper mechanical damage had occurred on the tube sheet. SÄKAPHEN fixed the damage by applying its new fully machinable Ceramoclad 221 to level out any deep cavity and, subsequently, its cold-cured epoxy paint HR 60 Extra TG as the top coat. The whole operation was done in the refinery’s metal workshop.
For every lining and coating requirement on your heat exchangers, SÄKAPHEN is always the right choice partner for protecting your assets!
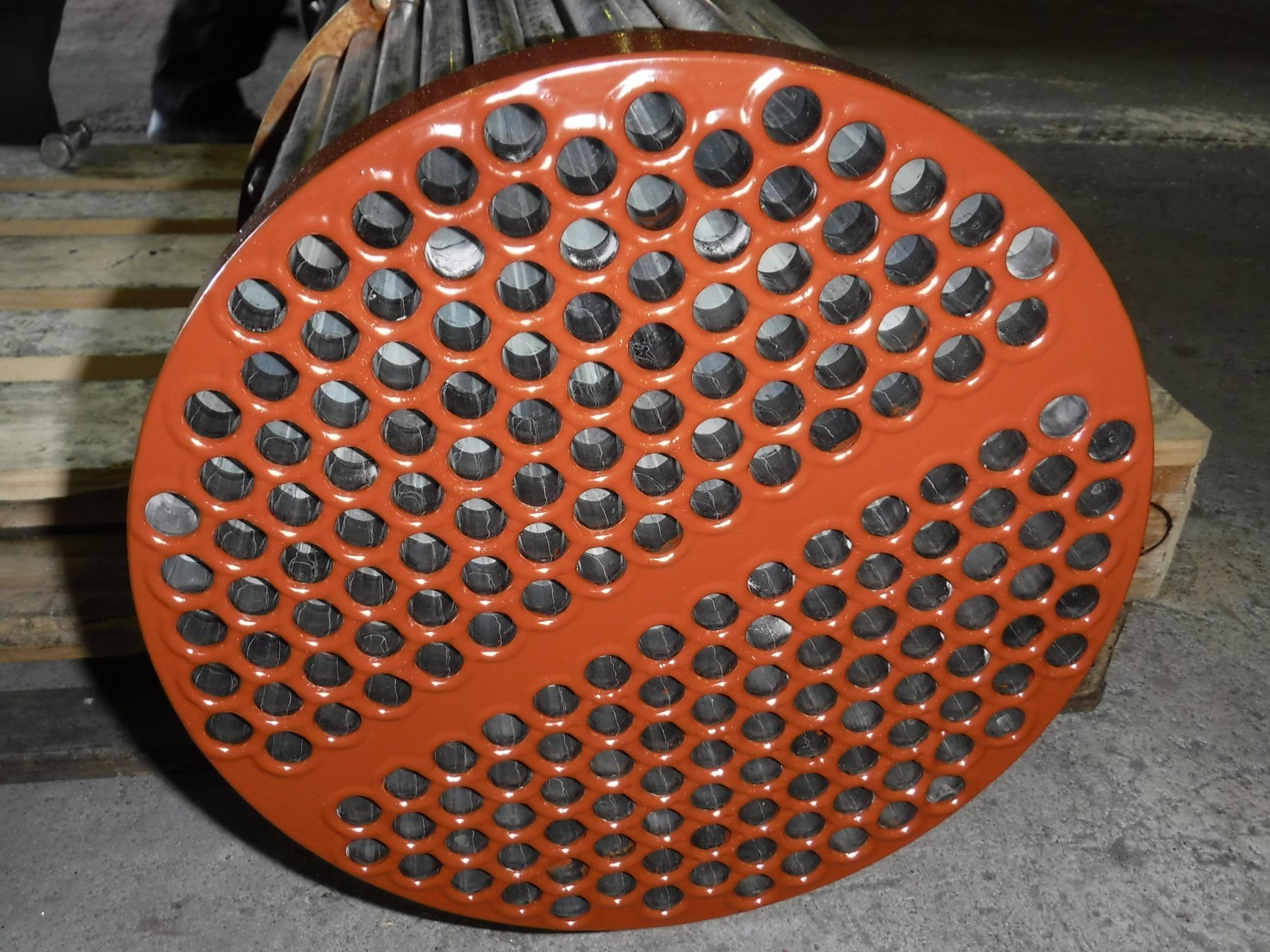

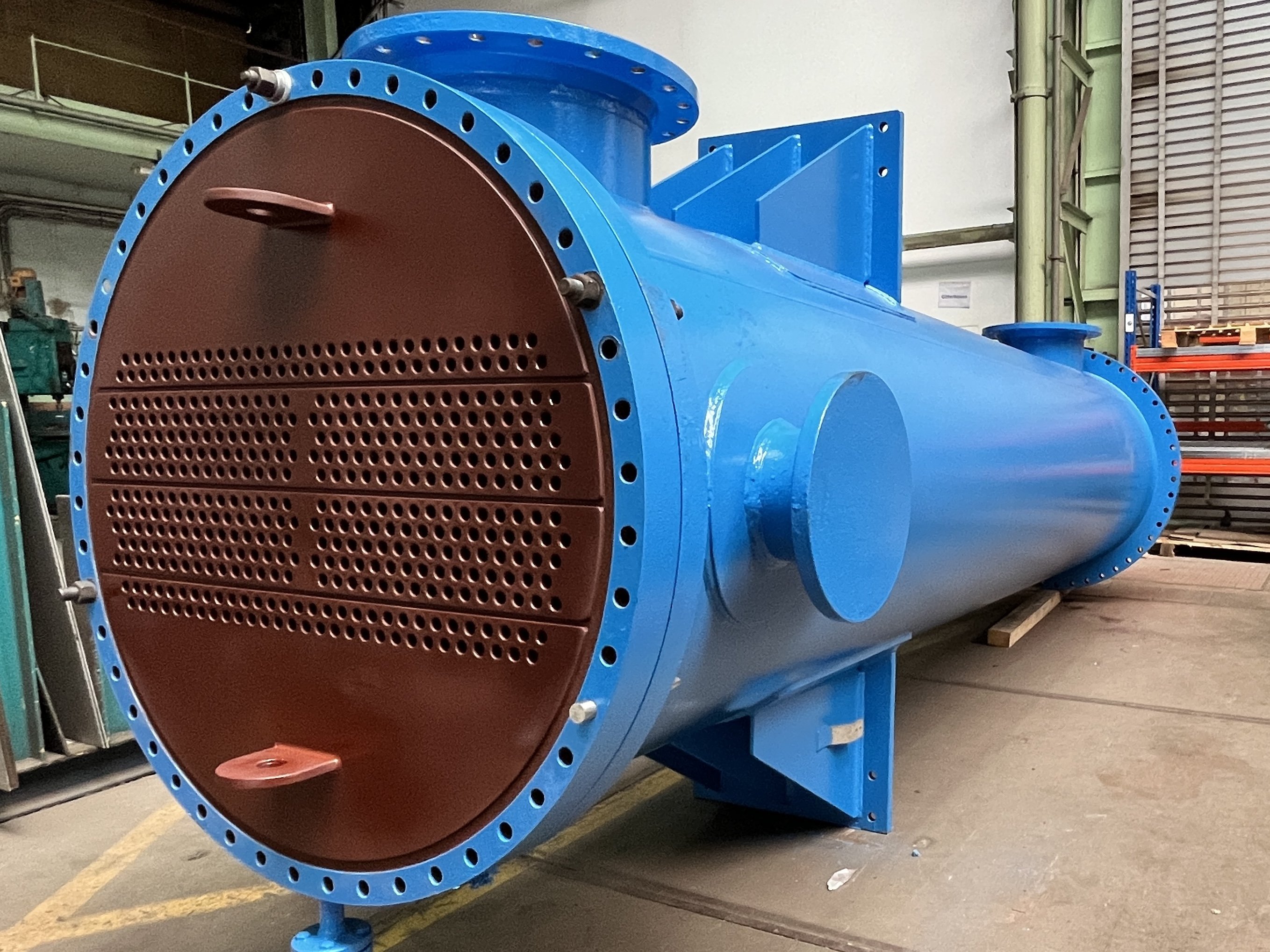